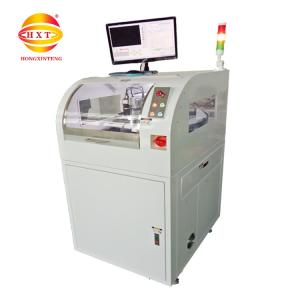
Add to Cart
PCB Depaneling Machine Split Circuit Board Pcb Separators Substrate Splitting Machine HXT-2500S Milling Cutter Machine PCB Board Cutting Machine
HXT-2500S Milling Cutter Separator is a device that uses high-speed rotating milling cutter to separate multi-piece PCBs according to the programmed path. Widely used in digital, communication, lighting and other fields. Improve the defects of manual board breaking, V-CUT, stamping, etc., improve quality and reduce scrap.
1. It adopts the bottom suction mode, which conforms to the theory of free fall, and has a good dust collection effect.
2. The substrate is fixed more firmly during cutting, avoiding the cause of poor basic positioning The cutting accuracy error.
3. Made of special jigs, easy to fix the products to be cut, to ensure high-precision products degree cutting requirements.
4. When cutting, the front part of the main shaft is equipped with an antistatic generator to continuously blow air, reducing the high Static electricity is generated when the high-speed spindle is cutting, which can prevent parts from being damaged by static electricity.
5. Safety doors are used to reduce noise and dust and improve safety.
6. The vacuum cleaner is equipped with a dust collection box (it can be cut according to the production capacity or when dust is collected) scheduled maintenance).
Negative pressure bottom suction device, built-in one, efficient and clean to solve the problem of dust collection
Negative pressure bottom suction structure is adopted, the air outlet is located under the carrier board jig, so that negative pressure is formed inside the jig, and the dust generated during cutting board can be easily removed; the drum type dust removal structure is built in the bottom of the machine, which perfectly solves the problem of cutting board It achieves small space and low noise production, and the energy consumption is lower than 1/2 of similar equipment, saving the limited production space of the workshop.
Function item | Hardware requirements |
X, Y axis cutting speed | 0-100mm/s |
X, Y, Z axis driving speed | X, Y axis at least 1000mm/s, Z axis at least 750mm/s, driven by servo motor |
Machine Repeatability | ±0.01mm |
Working area (machinable stroke) | X: 300mm, Y: 350mm, Z: 0-50mm |
Cutting PCB thickness range | 0.5-2mm, or a larger range |
Cutting accuracy | ±0.01mm |
Cutting capacity | Capable of cutting straight lines, arcs, circles, L-shape and U-shape |
Tool changing system | Manual tool change system, tools required (original machine delivery) |
Tool Wear System | Intelligently set the number of cutting segments of the milling cutter (5 segments) |
Number of Tables | 2 |
Table function | Parallel Table operation mode; the device can realize the linkage function of two Tables |
Spindle speed | MAX60000rpm |
Spindle Cooling System | need air cooling |
Dust collection method | Lower dust collection |
Working power | 380V, 50HZ |
Air supply | Above 0.45Mpa |
Safety devices | Use security doors or sensors |
Aircraft model | Offline model, manual loading and unloading of PCBA |
Automatic fault detection maintenance mode | The system has self-diagnosis function, real-time error information display, can intuitively query the status of each IO port of the device, and is easy to troubleshoot. |
Computers and Operating Systems | Industrial computer, Windows7 or above. |
Software rights management | Password protection, enter the corresponding operation interface according to the authority, and protect the important parameters of the system. |
Programming | Visual interface, unlimited cutting point capacity of a single program, dynamic simulation of cutting path. |
Mark point automatic calibration function | With Mark point automatic calibration function |
fixture | Universal fixtures are available |
Noise control | When running, the noise is less than 60 decibels (measured at a distance of one meter from the device) |
Warranty cycle | The whole machine is 1 year or more, the spindle is recommended to be more than 2 years and the maintenance service of the spindle is provided for 3000 hours within the warranty period. |
Technical support and training | Provide equipment operation, programming, hardware maintenance, maintenance training services; program permanent free upgrades. |
Widely used in electronics manufacturing, consumer electronics, automobile electronics, communications equipment, aerospace, medical equipment, LED lamps, computers and peripherals, smart home, smart logistics, miniature and high power ratio electronic devices.